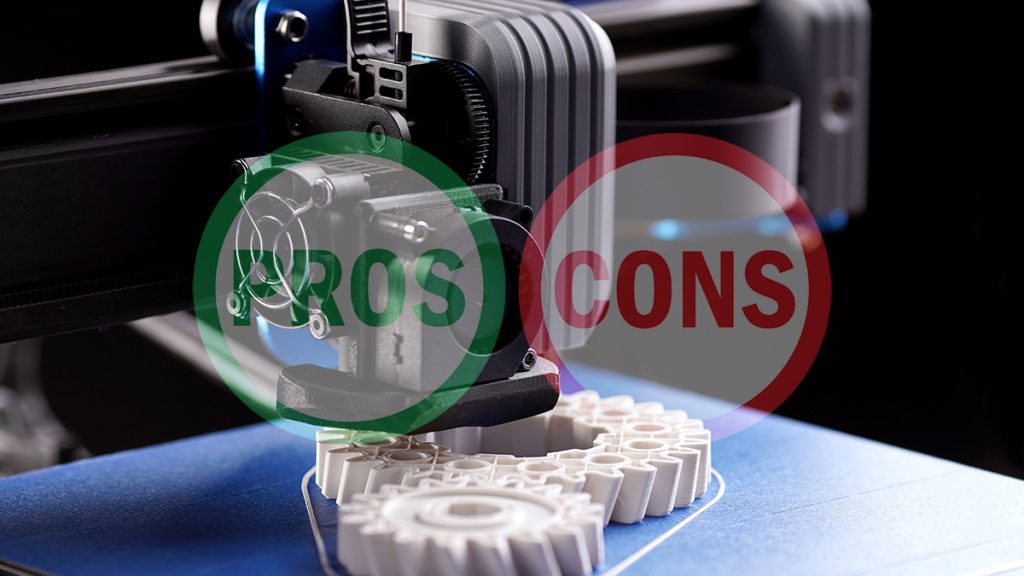
Over the past decade, 3D printing has emerged as a revolutionary technology that has disrupted various industries, including the aerospace industry. 3D printing, also known as additive manufacturing, is a process that involves creating three-dimensional objects by adding materials layer by layer. This technology has transformed the way aerospace manufacturers design and produce parts, leading to a reduction in lead time, improved efficiency, and reduced costs. Looking at it from another perspective, as with any technology, 3D printing has its benefits and drawbacks. In this article, we explore the benefits and drawbacks of 3D printing in the aerospace industry and how it is different from non-sustainable technologies.
Good to some extent
One of the most significant benefits of 3D printing in the aerospace industry is its ability to produce complex and lightweight parts. Traditionally, aerospace manufacturers had to rely on time-consuming and expensive machining processes to create complex parts. With 3D printing, designers can create complex geometries that would have been impossible with traditional manufacturing methods. Additionally, 3D printing enables manufacturers to create parts with reduced weight, which is crucial in the aerospace industry, where every gram counts.
Another significant advantage of 3D printing in the aerospace industry is its ability to produce parts on-demand. In the past, aerospace manufacturers had to maintain large inventories of spare parts, which were expensive to store and maintain. With 3D printing, manufacturers can quickly produce spare parts when needed, reducing lead time and costs.
3D printing also offers greater design flexibility, allowing manufacturers to create parts that are tailored to specific applications. This has led to the development of new and innovative designs, such as lattice structures, which offer superior strength and weight reduction.
Many non-sustainable technologies are still used regularly, so what makes 3D printing in the aerospace industry any different? Why are they not using it? Apart from non-sustainability, while 3D printing has come a long way in terms of the quality of the parts produced, there is still a risk of defects and inconsistencies, which could compromise safety. Governments look at the overall drawbacks not just if it’s sustainable or not. Another significant disadvantage is the high cost of 3D printing equipment and materials. While the cost of 3D printing has decreased over the years, it is still significantly more expensive than traditional manufacturing methods.
Final Thoughts
Ultimately, the sustainability of 3D printing in the aerospace industry will depend on a range of factors, including the materials used, the production process, and the end-of-life disposal of products. While there are challenges to overcome, 3D printing has the potential to offer significant benefits to the aerospace industry, and it is up to industry stakeholders to work together to find sustainable solutions that balance the benefits of 3D printing with the need to protect the environment.
Inside Telecom provides you with an extensive list of content covering all aspects of the tech industry. Keep an eye on our Intelligent Tech sections to stay informed and up-to-date with our daily articles.