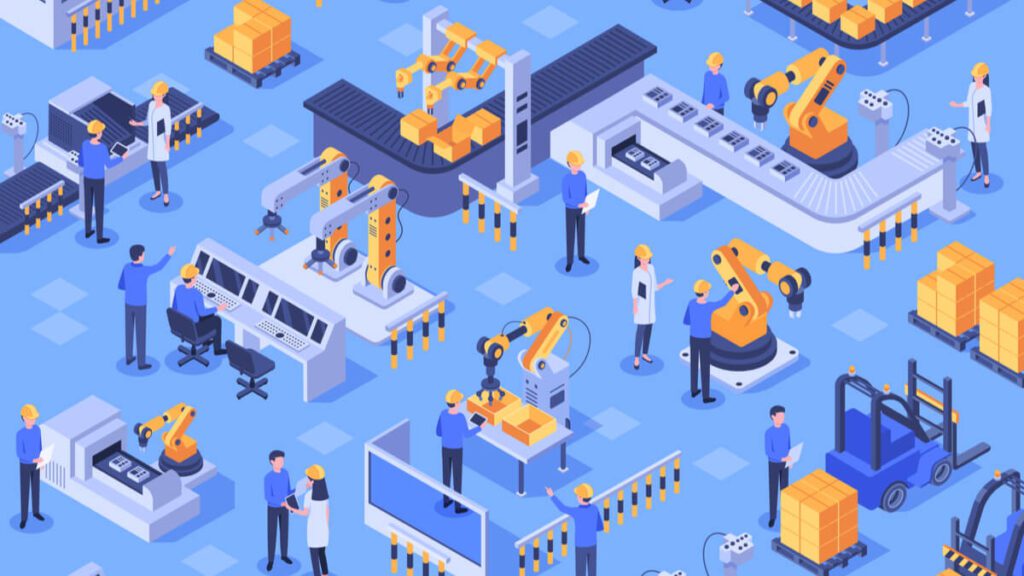
Connecting people, data, machines, and supply chains is crucial for the success of the digital transformation that is accelerating the pace of business innovation.
Smart factories are fast becoming a reality, with increasing amounts of data being processed by machines on the factory floor. But connecting these with global teams and dispersed supply chains is often still proving a challenge.
Existing connectivity solutions are complex, consisting of layers of legacy solutions that are overly reliant on physical connections. The promise of Wi-Fi and 4G was never realised as the solution was unable to deliver the guaranteed bandwidth and latency to address factory-wide applications.
The reality is that enterprises have hard wired connectivity to ensure the service level availability required for mission-critical applications – resulting in a spaghetti of cabling and network hardware that is complex, difficult to manage and resistant to innovation.
The current roll-out of 5G and Wi-Fi 6 has the potential to solve this conundrum by delivering bigger pipes with lower latency covering larger distances. This capability is further enhanced by 5G private networks that are able to dedicate bandwidth to the enterprise to deliver the required quality of service.
This will allow companies to break free of the handcuffs of the spaghetti network and move towards a wireless experience, as it drastically simplifies the network infrastructure and paves the way to faster and more cost-effective adoption of technological innovation on a factory-wide basis.
But this is only part of the story.
The emergence of 5G and Wi-Fi 6 is not the panacea in isolation and requires other enabling technologies, such as server-side rendering and edge computing, to realise the potential step change in efficiency gains.
Edge computing will allow data to be processed closer to the application – significantly reducing latency, which is critical to enabling extended reality (XR) use cases. It is estimated that, by 2025, 75 percent of enterprise data will be processed at the edge, compared with only 10 percent today.
Additionally, server-side rendering will move the computing processing required for XR to the cloud to be delivered via streaming solutions at a level of fidelity equivalent to the tethered experience today.
This will materially lower the economics for the roll-out of XR services as the graphics processing unit (GPU) costs are efficiently spread across all users – and ultimately will lead to more practical and cheaper XR headsets as graphics processing moves off the device and into the cloud.
The combination of 5G, edge computing and server-side rendering will enable greater use of XR solutions at a significantly lower cost.
This vision for the future is happening today. Vehicle battery manufacturer Hyperbat – a joint venture between Williams Advanced Engineering and Unipart Manufacturing – recently announced a world-first untethered 5G native experience that will allow design and engineering teams to walk around and interact with a 3D life-size model in real time via a 5G-enabled virtual reality (VR) headset, and without the constraints of a physical connection.
Large companies, in particular, tend to have very complex technical architectures that have grown incrementally over time – making it difficult to change existing processes and add new functionalities.
Additionally, when they try to introduce innovations such as immersive technology, they face very high barriers to adoption because it’s hard to move beyond a demonstrator concept to scale the production solution. A key success factor for XR adoption is to integrate and embed the solution into the existing enterprise processes – not the other way round.
The solution starts with the data – the common denominator between technology, methods, tools, processes, and people. Using data to make the right decisions at the right time is crucial to success, saving businesses large amounts of time and money.
In the automotive industry, for example, a poor decision that leads to downtime for a production line costs, on average, £15,000 per minute.
The technology enablers, when combined with real-time collaboration and XR, are able to bring geographically dispersed teams together, combine multiple data sources and provide a contextual understanding of the factory floor to deliver a new way of working that will deliver a paradigm improvement in operational efficiencies. The following are examples of how these combined capabilities can be leveraged today.
XR design review
The design process is enhanced by the seamless ability to move between the computer-aided design (CAD) application and the XR experience to review a model on a 1:1 scale basis in situ. It is imperative this real-time immersive experience is collaborative as remote working is now a reality and a wide range of stakeholders need to be consulted and involved in signing off a design.
The ability to align the various stakeholders by removing ambiguities through leveraging XR technologies is key to reducing inefficiencies downstream.
Design to manufacturing handover
The flow from design to suppliers to manufacturing and assembly can be a bumpy one, resulting in many iterations and opportunities for missed communication.
Providing the manufacturing, supplier, and assembly teams with the ability to review the designs at 1:1 scale earlier in the process reduces iterations, lower waste, avoid future maintenance issues and improve time to market.
It is cheaper to fail in software than in the physical world.
Virtual commissioning
The planning and deployment of robotic machinery can be a very complex and time-consuming process. Mistakes are not only potentially hazardous but also costly in terms of damaged equipment and production line downtime.
The ability for engineers to work together in immersive environments and view robotic simulations at full scale in real time not only speeds up the implementation time but also ensures that any robotic errors in the assembly line can be reconfigured virtually to materially reduce the downtime.
Remote expert assist
Accessing an expert on-site for diagnosing and fixing complex machinery on the factory floor is often time consuming, expensive, and sometimes impossible now due to Covid-19 restrictions. With XR collaboration solutions, remote experts can be brought into a spatial environment to help address mechanical problems in the field.
This solution brings both the data and people together in real time to deliver significantly quicker diagnostics and restoration times, while allowing a centralised team of experts to support efficiently dispersed teams around the world.
Augmented ergonomics and assembly
The ability to overlay the hologram of a design onto a physical asset – a process called digital sleeving – has a broad range of applications from augmented ergonomics through to augmented assembly.
Integrating real-time collaborative XR processes onto the factory floor to seamlessly bring disparate data and dispersed teams together will drive a new way of working that will determine the success of the businesses of the future.
by Karl Maddix, CEO of software scale-up Masters of Pie