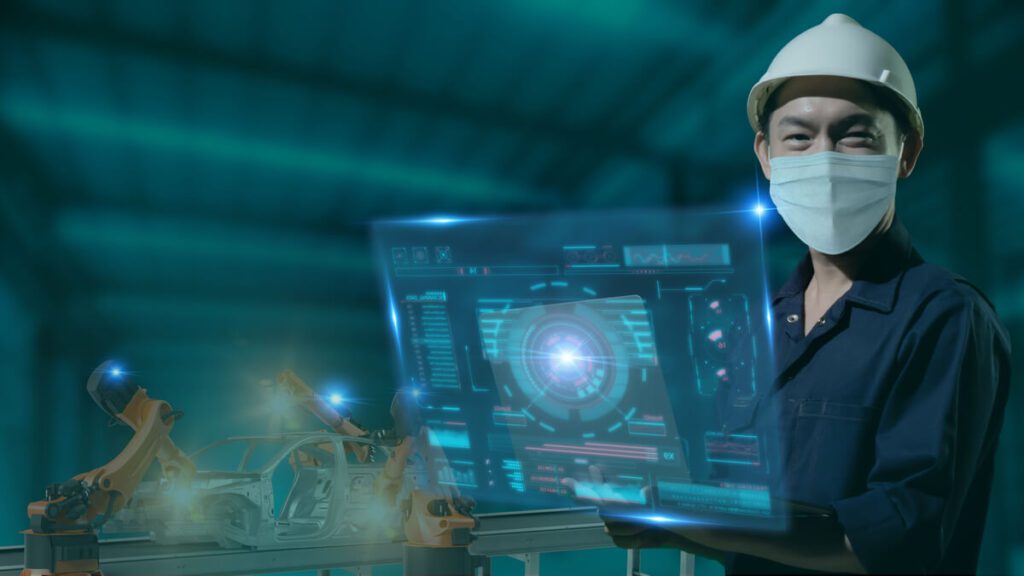
As the current pandemic continues, we see the effects of COVID-19 on productivity and costs in the manufacturing sector. Mandatory lockdowns have caused major disruptions with assembly lines forced to curtail or halt operations due to a lack of workforce and parts. Protecting employee health has become an even greater concern during the outbreak.
However, there is a silver lining. Manufacturers can adapt to the changes, following steps to ensure faster recovery when conditions improve.
Importance of cloud and 3D printing prospects
The pandemic has highlighted the importance of technology for business continuity. Digital technology has helped create a sense of normalcy via online collaboration.
Research indicates that companies that are digitally mature have higher resilience especially in areas like employee engagement and supply chain operations. The manufacturers that have moved critical business applications to the cloud are enjoying a smoother functioning as employees can access what they need from the comfort of their own homes. Enterprises that have invested in advanced analytics have adapted to the changes far better.
Not only did the pandemic change the norms for remote working, it is also accelerated the move toward digital manufacturing. 3D printing technologies will now be pursued more aggressively given that additional use cases have emerged. 3D printing technology has proven to be an added value in the manufacturing sector as it allows for the rapid conversion of designs to finished products, even for challenging designs.
What is important to note is that manufacturers should hurry in moving their systems and data to the cloud if they haven’t already done so. Cloud-based solutions allow businesses to scale costs to revenues and hit a tighter demand-supply agility.
Maintaining employee motivation
No matter the advances made in technology, ultimately, its humans who make the decisions and perform the work. The current pandemic has created personal health concerns – a never seen before spike in unemployment – and anxiety regarding the future. To try and keep employees motivated, several organizations announced a 90-day window of no layoffs, using this period as an opportunity to reskill their employees for post-pandemic needs.
Large enterprises must aim to protect health and the employment of their employees. They can do so by using automation to decrease risk infection and to improve their operations. With more people working remotely, and as the flow moves towards digital as a primary mode of interaction and transaction, it has become imperative to foster an operating environment that ensures workforce health and productivity. This will also be critical to attract and retain the best employees as conditions improve.
The need for a digital nerve center
The pandemic has ignited a heightened awareness for more efficient analysis and response.
This detect, analyze, respond framework is essential for an enterprise to exist and thrive. A suggestion would be to establish a nerve center for the organization that that can collect data from multiple types of equipment to help form clear recommendations later. When the crisis fades, this nerve center concept will be extended to become the digital brain for the entire enterprise.
The pandemic has highlighted the importance of supply chain management and remote work, it also gives players in the manufacturing sector new meaning and perspective on how to run their operations.