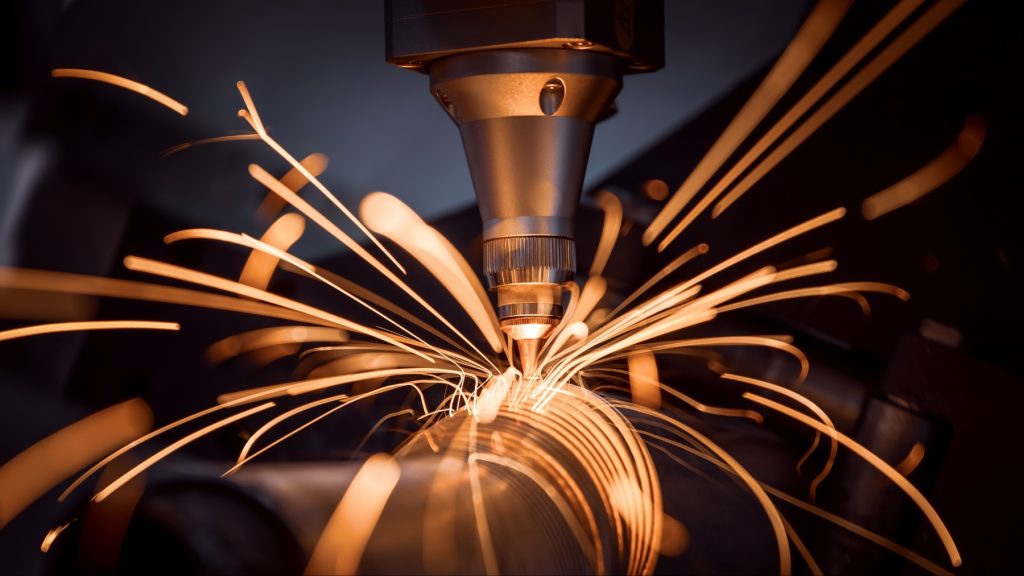
Best Metal is giving steel a green face, as its molten oxide electrolysis produces steel using electricity.
- Steel is currently produced using blast furnaces fueled by coal, resulting in substantial carbon emissions.
- MOE technology uses electricity instead of coal, producing only oxygen as a byproduct.
- Each MOE cell can produce up to 10 tons of metal daily.
Boston Metal figured out how to make steel using electricity, pushing metal-making and associated industries to go green.
Boston Metal is a spin-out of the Massachusetts Institute of Technology (MIT), founded by MIT Professors Emeriti Donald Sadoway and Antoine Allanore in 2013. After years of hard work and research, they are finally going commercial with their Molten Oxide Electrolysis (MOE) technology.
Steel is the world’s most important engineering and construction material, used in cars and construction products, refrigerators and washing machines, cargo ships, and surgical scalpels. However, steelmaking involves blast furnaces using coal, which makes it highly carbon-intensive and, therefore, not eco-friendly. According to the International Energy Agency (IEA), in 2022, the total CO2 emissions from the iron and steel sector is 1.41 tons of CO2 per ton of steel produced.
Boston Metal Chief Scientist and former MIT postdoc Guillaume Lambotte confirmed that “Steel produces around 10% of global emissions.” He goes on to talk about how every sector is looking to play its part in the fight against climate change. “So, the steel industry is really looking hard for viable technology solutions. People are ready for new approaches,” he said.
Boston Metal’s solution for green steel, the MOE technology, relies on electricity rather than coal, to make the in-demand metal. It eliminates several steps in the process, and its only byproduct is oxygen. The team runs an electric current through iron ore mixed with a liquid oxide electrolyte at around 1,600 degrees Celsius (2,912 Fahrenheit), splitting the iron oxide into pure liquid iron and oxygen.
Each MOE cell is capable of producing up to 10 tons of metal daily, depending on the electric current supplied.
Boston Metal’s MOE technology could potentially outperform green hydrogen-based steel production. The latter is expensive and is limited by the need for high-grade iron ore. However, the former can process lower-grade ores, which provides a significant economic advantage. While the costs are still uncertain, it could potentially lower costs and increases the accessibility of green steel.
Its potential to be more affordable than traditional methods could favor underdeveloped countries. If MOE proves to be less expensive, it will enable these nations to leverage a technology that not only reduces the environmental impact of steel production but also allows for the creation of robust and sustainable infrastructure. What will follow is easier access to better transportation, housing, and public services, all while aligning with global sustainability goals. As a result, the citizens’ quality of life improves. Not to mention that the new infrastructure, courtesy of green metals, catalyzes economic development.
Inside Telecom provides you with an extensive list of content covering all aspects of the tech industry. Keep an eye on our Tech sections to stay informed and up-to-date with our daily articles.