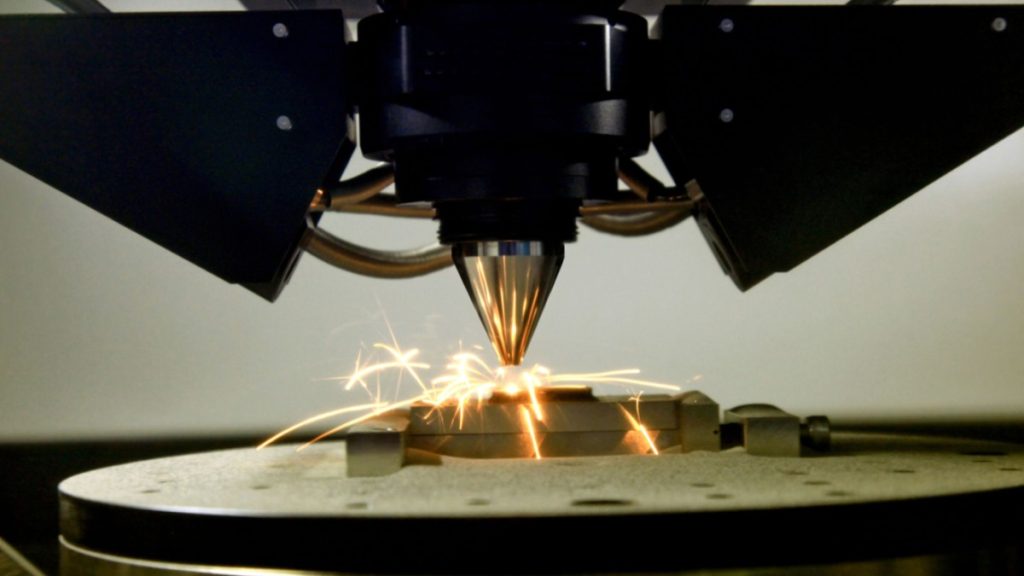
A group of researchers have 3D printed a double stage, nanostructured high-entropy compound that surpasses the strength and flexibility of other cutting edge additively produced materials. This advancement could prompt better execution parts for applications in aviation, medication, energy, and transportation. The work was finished by specialists from the University of Massachusetts Amherst and the Georgia Institute of Technology. It was driven by Wen Chen, right hand teacher of mechanical and modern designing at UMass, and Ting Zhu, teacher of mechanical designing at Georgia Tech, will be distributed today (August 3, 2022) in the diary Nature.
High entropy compounds (HEAs) have become progressively famous as another worldview in materials science throughout the course of recent years. They are contained at least five components in close equivalent extents and proposition the capacity to make a close boundless number of exceptional mixes for composite plan. Conventional combinations, for example, metal, treated steel, carbon steel, and bronze, contain an essential component joined with at least one minor components.
Recently, 3D printing, sometimes referred to as additive manufacturing, has become a potent strategy for material creation. Large temperature gradients and rapid cooling rates, which are not easily accessible by conventional means, can be produced using laser-based 3D printing. However, “the potential of harnessing the combined benefits of additive manufacturing and HEAs for achieving novel properties remains largely unexplored,” says Zhu.
Chen and his group in the UMass Multiscale Materials and Manufacturing Laboratory consolidated a HEA with a cutting edge 3D printing strategy called laser powder bed combination to foster new materials with uncommon properties. Since the cycle makes materials soften and set quickly when contrasted with customary metallurgy, , “you get a very different microstructure that is far-from-equilibrium” on the parts made, Chen says. This microstructure seems to be a net and is made of rotating layers known as face-focused cubic (FCC) and body-focused cubic (BCC) nanolamellar structures implanted in microscale eutectic states with irregular directions. The progressive nanostructured HEA empowers co-usable disfigurement of the two stages.
“This unusual microstructure’s atomic rearrangement gives rise to ultrahigh strength as well as enhanced ductility, which is uncommon, because usually strong materials tend to be brittle,” Chen says. When compared to conventional metal casting, “we got almost triple the strength and not only didn’t lose ductility, but actually increased it simultaneously,” he says. “For many applications, a combination of strength and ductility is key. Our findings are original and exciting for materials science and engineering alike.”
“The ability to produce strong and ductile HEAs means that these 3D printed materials are more robust in resisting applied deformation, which is important for lightweight structural design for enhanced mechanical efficiency and energy saving,” says Jie Ren, Chen’s Ph.D. student and first author of the paper.
Zhu’s gathering at Georgia Tech drove the computational displaying for the exploration. He created double stage gem pliancy computational models to comprehend the robotic jobs played by both the FCC and BCC nanolamellae and how they cooperate to give the material added strength and pliability.
According to Zhu, the results of the simulationed showed surprisingly high strength “yet high hardening responses in the BCC nanolamellae” which are essential for achieving the alloy’s exceptional strength-ductility synergy. This mechanistic knowledge serves as a crucial foundation for future development of 3D-printed HEAs with outstanding mechanical characteristics.
In addition, 3D printing offers a powerful tool to make geometrically complex and customized parts. In the future, harnessing 3D printing technology and the vast alloy design space of HEAs opens ample opportunities for the direct production of end-use components for biomedical and aerospace applications.